by Eric Meier
Have you ever had a project that was coming along nicely up until the finishing step? You apply the polyurethane to the wood, and wait for it to dry. And wait. And wait. And finally, days, weeks, (or even months!) later, the finish has still not dried. What went wrong, and how do you solve this problem?
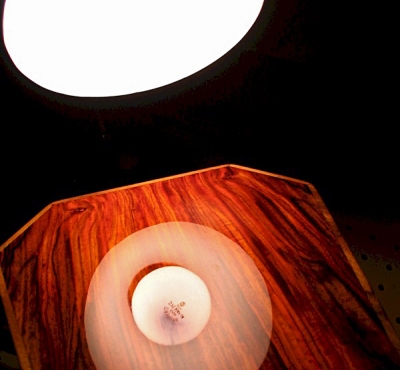
Before proceeding much farther, you should ensure that you are using a fresh and well-stored finish. Very old or improperly stored finishes may have difficulty curing. Also, many complications can arise between low-quality wood stains and polyurethane, so be sure to test on a scrap piece before any large project. If the finish seems to be drying on most regular wood surfaces, but it will not harden on an exotic wood, consider the following:
Why oil-based finishes do not dry on many exotic woods
Unlike many of the comparatively tamer domestic hardwoods that woodworkers in the United States, Canada, and the United Kingdom are used to working with, many trees in tropical climates have unique chemical compositions in their heartwood extractives. Many of these compounds are readily soluble in various solvents found in finishing agents, (something that’s evident when wiping a wood with a solvent prior to gluing).
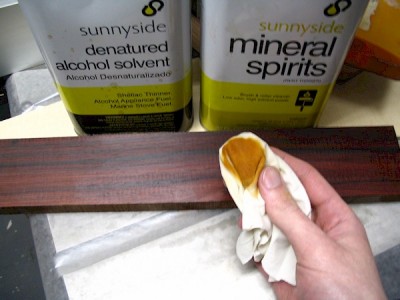
What goes wrong
Oil-based finishes, such as polyurethane, are reactive finishes. That is to say, they undergo a chemical reaction as the solvent in the finish evaporates—ultimately causing the finish to cure and harden. The problem occurs when compounds in the wood (more specifically, antioxidants) leach into the applied finish, preventing this chemical reaction from ever occurring. Without the necessary reaction, the finish remains tacky indefinitely.
What can be done?
If you have already applied polyurethane to a bare exotic wood surface, there’s not much that can be done to redeem the existing finish. You’ll more than likely have to scrape, sand, wipe, or otherwise remove the existing finish as best you can, and start over from square one. A mineral-spirits soaked rag can usually remove the bulk of the finish.
Since reactive finishes simply can’t cure on exotic woods, what is needed is an intermediate coating between the bare wood and the final polyurethane topcoat. In contrast to reactive finishes, there are also evaporative finishes. Evaporative finishes differ from reactive finishes in that they are generally simpler, and do not undergo any sort of chemical reaction to cure or harden. A resin or other material is dissolved in a solvent, and once the solvent evaporates, a thin film is left behind. In the case of evaporative finishes, the antioxidants may still leach into the finish, but this fact is moot, as the solvent will still evaporate, and the finish will inevitably harden.
A couple examples of evaporative finishes would be nitrocellulose lacquer and shellac. In a number of low-wear applications, either of these two finishes could legitimately be used as a substitute for polyurethane in a completed project. However, neither have quite the same durability and scratch-resistance as polyurethane, so it may be preferable to simply use an evaporite finish as an intermediate layer between the raw wood and the topcoat. For this purpose, shellac greatly excels in suitability.
Shellac is your friend
Shellac makes an excellent sanding sealer and intermediate coat between bare wood or stains/colorants and the final topcoat(s). There’s an adage among woodworkers about shellac that may not even overstate its usefulness as a wood finishing agent:
Shellac sticks to everything, and everything sticks to shellac.
This is as close to a silver bullet as woodworkers are going to get. Simply apply a few coats of dewaxed shellac to seal the antioxidants in the wood, and then apply the topcoat of your choice. For particularly oily woods, two to three coats may be necessary to ensure that there is no interference with the heartwood extractives below.
Sourcing shellac
Shellac is sold in a variety of forms, and has generally received an unjustifiably bad reputation. This is due to its generally short shelf life (about a year once mixed), at which point, ironically, it also begins to have difficulty fully hardening. But freshly-mixed shellac will dry hard and will do so very quickly.
Premixed varieties of shellac can be highly variable in quality. Zinsser produces a line of shellac finishes available in most hardware stores which have their date of manufacture printed on the bottom of the can, helping to ensure that you get a fresh product. The most relevant product to finishing is Zinsser’s SealCoat, which is simply a #2 cut of shellac, (and despite its name, can be used as more than a sanding sealer; it can also be used as a standalone wood finish).
To obtain optimum performance from shellac, it’s best to mix your own. Shellac is about the simplest wood finish to make, as it contains only two ingredients: shellac flakes, and denatured alcohol solvent (DNA). Alcohol solvent is readily available at any hardware store, and shellac flakes can be purchased at woodworker retailers, as well as online. When shellac is mixed, the ratio of flakes to DNA is known as its cut, and is measured in pounds per gallon. So if you mixed three pounds of shellac flakes into a gallon of DNA, you would have a three-pound (#3) cut of shellac.
Simple recipe for homemade shellac sealer
1 cup (8 oz). of denatured alcohol solvent
1 oz. of dewaxed blonde shellac flakes
- Using a postal scale, weigh out one ounce of shellac flakes.
- Pulverizing the flakes in a dedicated blender can help accelerate the dissolution process.
- Pour alcohol into a small, sealable jar, and gradually stir in flakes. (A magnetic stirrer also works very well for this purpose.) Stir or shake jar every 10-20 minutes; flakes should dissolve within a few hours.
- This recipe will make a #1 cut of shellac, which will be a thin, very fast drying sealer that’s easy to apply with a brush or rag. Typically, the second coat can be applied just minutes after the first coat. (With subsequent coats taking slightly longer to dry.)
- For a #2 cut, as would be typical for building a wood finish film, simply double the amount of shellac flakes to 2 ounces.
- Mixing eight ounces at a time makes it easiest to calculate the pound-cut of the shellac: simply substitute ounces for pounds (i.e. 2 oz. of flakes equals #2 cut, 3 oz. equals #3 cut, and so forth.)
- Larger quantities can also be mixed for larger projects: just remember that shellac has a limited shelf life, and the fresher the shellac, the better.
Known problematic woods
Below is a non-exhaustive list of woods that have heartwood extractives that tend to interfere with the curing process of oil-based finishes.
- Blackwood, African
- Blackwood, Australian
- Bloodwood
- Bocote
- Cedar, Eastern Red
- Cocobolo
- Cumaru
- Ebony
- Goncalo Alves
- Ipe
- Katalox
- Kingwood
- Lignum Vitae
- Lignum Vitae, Argentine
- Macacauba
- Padauk
- Pau Ferro
- Purpleheart
- Rosewoods
- Teak
- Tulipwood
- Verawood
- Ziricote
See also:
- Gluing Oily Tropical Hardwoods
- Preventing Color Changes in Exotic Woods
- Wood Finishing: What Works When
Are you an aspiring wood nerd?
The poster, Worldwide Woods, Ranked by Hardness, should be required reading for anyone enrolled in the school of wood nerdery. I have amassed over 500 wood species on a single poster, arranged into eight major geographic regions, with each wood sorted and ranked according to its Janka hardness. Each wood has been meticulously documented and photographed, listed with its Janka hardness value (in lbf) and geographic and global hardness rankings. Consider this: the venerable Red Oak (Quercus rubra) sits at only #33 in North America and #278 worldwide for hardness! Aspiring wood nerds be advised: your syllabus may be calling for Worldwide Woods as part of your next assignment!
How did you get the wood on the first picture of the article to be so shiny?
I used a finishing technique that’s very similar to how guitars are finished. Basically build up ten or more layers of finish (in this case, shellac), then sand it completely level, and polish it with progressively finer grits of buffing compound.
I apologize in advance for my English… (I am not directly concerned even if I am passionate about wood and a professional musician) perhaps this is ignored but there remains an artisanal know-how (often family stories) which has become very rare in the world of veneer production, that by sawing offering exceptional rendering and quality used in very high-end marquetry or in the repair of collector’s items… maybe you will have the opportunity to do a report etc. during a visit to Paris ? ;-) remains a know-how to defend… one of the famous and rare small companies using this… Read more »
Hi, we have a client with an ebony wood exterior door that is showing signs of wear after 10 years. What would you suggest would be the best way to restore this sentimental piece?
Hello
I have ipe through out my home. There doesn’t seem to be any flooring people in my area that are familiar with it. It is getting close to needing to be refinished. If I am understanding this article correctly I need to have the flooring contractor sand the existing floor and apply 2-3 coats of shellac then finish with a topcoat of polyurethane. Is there a recommended poly for this application?
I doubt a flooring dealer would ever use shellac, there are probably much more job-specific industrial sealers available to them. This advice was meant solely for hobbyists doing smaller projects like furniture or musical instruments.
I have a 4’x4′ piece of Guanacaste
It has been sanded & ready for finish. I am using Rubio Monocoat finish. I was going to seal it first. Normally I fine sand after sealing. How many coats of sealer do you recommend? And still sand with fine grit in between?
Does Teak oil work on Katalox and other exotic hardwoods?
Eric, What a great site and book! I am looking to refinish this (Indonesian?) tropical hardwood rough sawn table. The damaged part shows the blonder natural wood, as opposed to the red ruddy finish. It is extremely heavy/dense. Apparently imported in early 2000s. Many thanks.
I have a custom built cantilevered corner window built out of Mangaris and we’ve had it finished professionally twice and each time the finish has deteriorated on the exterior and is flaking off. The interior has remained beautiful and the window is north facing so is not getting significant sun exposure. As it’s an extremely hard wood the previous finisher stated that it was just going to be a problem which I don’t quite believe. My husband would like to paint (yikes!) and I’m looking to keep the beauty of the wood. Please if anyone has recommendations as to what… Read more »
Hey Diane, It’s been a bit since you posted, but why not reach out, right? First off, I’m curious how often it has had to be refinished, because, unfortunately, wood exposed to the elements will never last forever with just a single finishing treatment. Boats are made for the water and every so often, they too must get taken out of service to get new paint. I had to look up Mangaris, which looks more like a brand name, and seems like it’s typically a type of dense tropical hardwood. Most of these, as mentioned in the article here, are… Read more »
How do you stop African redwood from bleeding ~ it’s a cutting board. And stains onto the counter.
you can add “milo” to the list of woods that prevent reactive finishes from finishing. i’ve got a piece i’ve been trying to finish for a year. wondering how many coats of shellac i need to apply before it’s safe to try something like GF’s Wood Bowl Finish again. one concern i have with using a barrier like shellac is that it might reduce the chatoyance of the wood. is that less likely to happen with lacquer?
I think it will depend on the # cut of shellac you are using. I prefer a thin 2# cut, so I usually need at least two, preferably three coats before I feel confident to top coat it with PU or similar finish.
I don’t see why the shellac would affect chatoyance more or less than any other finish. Are you using blonde shellac? Seems like the clarity should be just as good as anything else.
That is a great poster. I just ordered one. Can you help identify this wood I have
Possibly walnut? Hard to tell from the picture, can you get a closer shot?
Would you like it with oil or raw?
Here
Here
Hey, I have some rosewood sarking I’ve put up in my van, I’m getting such conflicting Info on how to dress it, can I apply a 2k acrylic polyurethane straight on top of it? Or do I need to seal it with shellac first? Cheers
So what cleaning product would be recommended for Tigerwood and what stain and seal coat?
Does anyone have any suggestions as to how I can solve a problem with my kitchen island bubinga wood countertop? I had a piece left over from a previous house. When I downsized and remodeled an old kitchen, they used the piece I had been storing to make the counter on a two level island. It looked great at first, but now it has small areas that are dry and grey. I have used tung oil to moisturize it, but the oil doesn’t eradicate the dry grey areas, although they do improve slightly. Should I consider lightly sanding these dry… Read more »
I would suggest sanding down the dry grey areas, and then applying tung oil, because to get the original color of the wood, generally you have to take off some material before you can see the original color. However, if you have a sharp scrub plane and a sharp smoothing plane, then it might be better to use a scrub plane to get the grey areas off, then use the smoothing plane to make everything flat. But if the piece is highly figured, then just use sandpaper to avoid tearout.
I got some ipe from a friend
Water doesnt bead up on it, it will slightly soak in. It came glued to make longer pieces. A test piece showed polyurethane coated great.
Can I do anything more to make sure the polyurethane works well
I need to remove a urethane spar finish applied in error to an old previously unfinished antique butternut door. What should I use? The paint is still tacky. I want to recover the original unfinished look.
Need some advice please – we have procured a substantial amount of Sneezewood, an indigenous tree to South Africa. It is very old however in excellent condition. It was cut down many years ago and has since been placed on the endangered list.
My questions are:
Is Sneezewood suitable to be in a pizza oven?
Is it easy to work with and good for making furniture?
Can it be burned indoor without affecting you negatively?
have had mahogany and tigerwood for years. sand and oil based poly is hard work but most beautiful outdoor desks ever. must be done every year
Going to be preserving a large IPE deck in very close proximity to the ocean. I have read all the comments above and would like some input on my plan- Sand the IPE, apply 2 coats Zinnser sealcoat, followed by 1 coat of Penefin oil; debating cutting the Penefin oil with linseed oil 3-1. Anyone have some advice or thoughts would be appreciated. The deck is large and I would prefer get this right for the client this time. For background info- I used a polyurethane the first time, and it blistered.
Thanks, David
Eric, very informative article. I am hopeful you can give me an opinion concerning exotic floor finishing job gone wrong. The wood species is Morado, from South America. It is unfinished in 5″ planks 3/4″ thickness. The finisher evidently did not have much experience with exotic species. I stained a sample of unfinished plank and opted for Cona by Varithane to deepen the coloration. They applied stain and duraseal polyurethane in semigloss and it turned into a tacky mess…on top of that the color is way oversaturated and in places almost looks painted (a waste of noble Morado). I told… Read more »
I probably wouldn’t use shellac for hardwood floors anyway. My point of reference is with smaller projects and furniture. I don’t have much experience by way of exotic hardwood flooring finishing. Surely there must be a product out there catering specifically to flooring to address these issues? Sorry I can’t be of more help.
I bet Tung or teak oil will do exactly what you want for your first step. Make sure everything is sanded well. When adding the 2nd coat of Tung or teak oil use 600 grit paper to get the oils deep into the wood. Hope this helps.
Jeremy,
Use Kotten Klenser Finish Feeder: https://www.amazon.com/Kotton-Klenser-Wood-Restoration-Cleaner/dp/B00LDCK8WO?SubscriptionId=AKIAILSHYYTFIVPWUY6Q&tag=duckduckgo-d-20&linkCode=xm2&camp=2025&creative=165953&creativeASIN=B00LDCK8WO
If you have a water stain from a wet cup under the finish, it will do miracles with that as well. Like anything, start with a small spot, rub it in, and it will work it self gone (keep rubbing). If that works, continue further in small amounts (not the whole piece at once).
Curious if anyone has suggestions for treatment of a milky white appearance of some spots on an Ebony musical instrument.
I have tigerwood deck , applied oil, and it’s greasy, uneven, it’ was prepped properly. Have tried Ipe oil and Thompson’s. All research I’ve done, and have followed. Is not working. It’s a big deck. Need advice desperately. Tha.ks in advance. It’s unsafe to walk on currently due to how slick it is. I’m in Midwest, and it gets full sun. It was installed in 2017. Then oiled for fist time with IPE. Now, June, 2018. prepped deck for yearly maintenance, and Thompson’s oil is bubbling in spots, slick in spots. Thanks in advance.
I have a very similar problem with my cumaru deck. I have used Ipe oil and Armstrong-Clark Wood Stain. Both left an oily finish that dulled and turned gray. I lightly power wash the scum off every year. I would really like to know what you recommend for a more durable sealer. Thanks!
What about using exterior UV resistant water based polyurethane on oily woods? Will water based polyurethane adhere to dewaxed shellac base? Does it still require dewaxed shellac sealer/primer coats? Thanks.
As far as I am aware, yes it will stick, and yes, you still need a coat of shellac between the wood and the finish. Even though it’s water based, I still believe it relies on oxidation for the finish to set up properly, and the antioxidants in the wood more than likely will interfere with that.
Help, we just bought a beautiful cocobolo bowl in Nicaragua! The bowl needs some type of oil or shellac! What can we use to finish off this beautiful raw bowl?
Thank you
Will A water-based polyurethane work on Ipe wood? Using the wood as a soffit on a pool house
Thanks
Hey all the guys asking about a great non toxic finish especially on exotics try odies oil. It was meant for exotics and it works great on exterior or interior applications. No extra steps involved on oily exotics.
THANK YOU for this recommendation!! What an amazing product, exactly what I was looking for
I recently tore up my back deck that I had put down a year prior because it turned black when I applied Penefin exterior deck finish to Tiger wood. I have ran it though a planer and would like to clear coat the raw wood and use as a head board. What indoor finish would you use that’s not so toxic.
Odies oil is your solution. Don’t waste your time with any other oils. They will not protect well at all especially on exotics.
Hi guys.. Need some advice here.. I wanted to make plywood out of rubber woods but I heard it requires a certain chemical to be mixed with the glue. Any idea what the chemical name is and where i can get it? Thanks a ton!
A little question, if you please. After 3 month after being applied, my shellac finish still gets fingerprints when tightly held several minutes by bare hands, especially hot hands (slight touching do nothing, though). Is it natural for shellac or it is just aforementioned 1-year shelf-life which is obviously long as expired?
I would say that sounds like an issue with the shelf life of the shellac — a process known as “esterification.” This is why I am an advocate of getting the shellac flakes themselves and mixing your own smaller batches of shellac from denatured alcohol as needed.
Thank you for quick reply! Fortunately, I have shellac flakes too. Is it good to use medicine-grade ethanol for prep? Commercial product which I used has isobuthanol as a medium – perhaps because of that, manufacturer guaranteed 2-year shelf-life, which is expired 1.5 years ago (yesterday I could not resist to use it again as a preliminary grain sealer for pine/spruce – it dries and sands, but somewhat sticky if touched with warm hands – like glossy magazine). Btw, is it good idea of still using this expired product when not alone? – I used this also as a sealer/intermediate… Read more »
Just to finish the story. After almost 3 years, I’ve finally realised that the shellac solution mentioned above contained turpentine in addition to isopropyl alcohol, oops! That is why it dissolved previous coats. So, finally I finished the bottle using it as a sealant/primer coat. Worked nice!
What exactly is ‘french polish’?
Help, help, help I fell in love with zebra wood and decided to do a kitchen island. the island is 4 ft wide by 11 feet long and about 1 and 3/4 inches thick. I need to waterproof it as there are two sinks in the island. We made two mistakes with finishing 1. the people making the counter sealed it with a floor sealer that was hazardous to your health. We sanded that off. 2.. we put mineral oil on it and mineral oil with a wax. It turned it to a reddish tone and more importantly there are… Read more »
From Timothy Gager = work with African woods and Central American woods. Learned Valuable Lesson Using ( Pink Ivory wood & Tullipwood ) sunlight will change the Color do not use Varnish. Go to a Good Boat Store tell them you want Marine Varnish for a Chris Craft Boat ( You will get best varnish that is UV Protected from the Sun. Some of these Older Boats go for $ 250,000 and you don’t put cheap varnish that changes color of the wood. Leopardwood / Redheart / Ziricote very dense will change in color using Varnish & Shellac Yellows !!!
Timothy, Great information. Finally! Yours is the first comment I’ve seen in hours of searching that addresses my exact concern. I have a large Parota (Guanacaste Tree) round that I’m making into an outdoor dining table. I’ve done some indoor things previously with Parota, which is not a dense wood, where I started with Tung oil to bring out the color, then did a coat of shellac sanding sealer, and then finished with a poly. However, I’ve been worried about the shellac sanding sealer over the tung oil for the outdoor table for just the reason you mentioned about yellowing.… Read more »
Thanks Eric. I made Two outdoors chairs using IME and finished them with ipe oil. I want to protec the chairs from the elements. Do you suggest a coat of shellac followed by 2-3 coats of varnish?
This article just saved my life. Pulling an allnighter to refinish my brand new product before it goes out the door.
Don’t use steel wool on any wood surfaces micro particles of steel can get in the wood then rust and tarnish the wood. Use brass wool or sandpaper.. Or cabinet scrappers for best results.
Choosing wood flooring for your home is a great investment. Unfortunately,
this kind of floors needs to be regularly maintained with refinishing to
preserve their beauty. Osmo Polyx Oils are one of the most recommended products
to be used for refinishing. It penetrates deep into the wood, making its core
strong, elastic, and healthy. It has natural component and harmless chemicals
that are safe for both man and animals.
Bright orange/red Padauk is my favorite accent wood. I now soak it in naphtha, dependent on thickness, after cutting it. Let dry then dip it into poly then hang to dry. I have not had a problem since doing this. Also if you want it to stay close to color you see mix a water based dye a shade or two less then the lightest hue in the wood, dye it with KEDA DYE while it soaks. The only issue is if the glossy poly is used it looks like plastic so go easy on the shine.
applied poly wipe on varnish to Padauk and it would not cure. after a week i removed it with
denatured alcohol. Did not have any shellac handy so i tried a water based varnish and it cured nicely in just a half hour. applied several coats and allowed to dry for 24 hours then sprayed it with poly, two coats that cured as expected. Nice glossy deep finish. Hope this helps someone else. Thanks for the help, great page of information.
richard i am making a large 6feet by 3feet paduak table top did your method give any problems
john russell
I applied poly over stained Goncalo Alves (Tigerwood). The poly cured without any issues. I’m not sure if the stain is protecting the poly from heartwood extractives, or if Tigerwood doesn’t have a lot to begin with.